Marquetry with Rolls-Royce
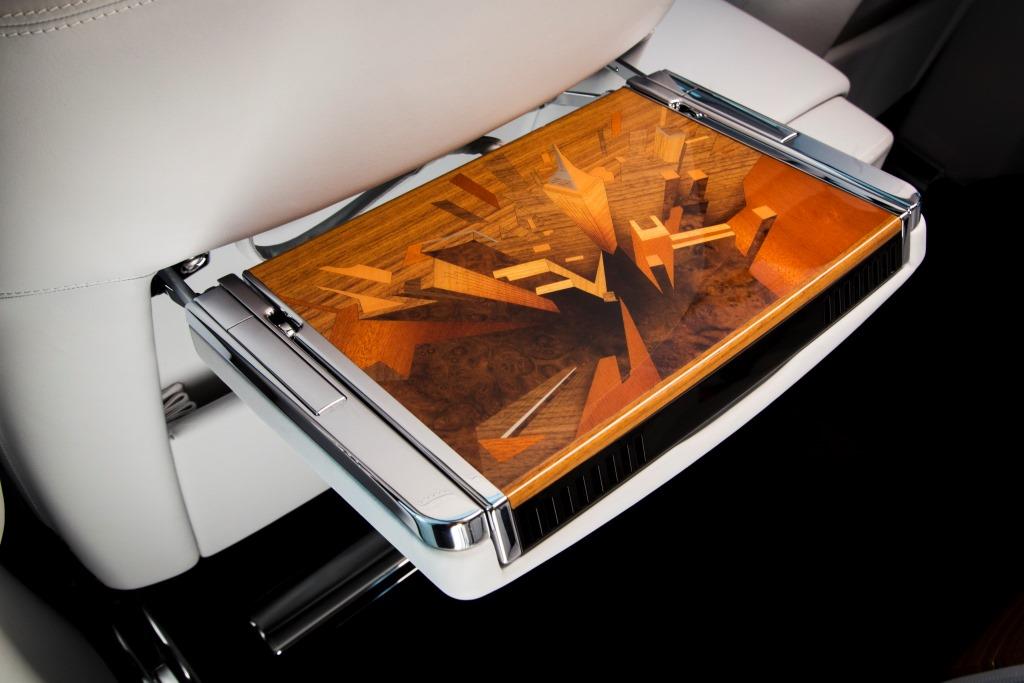
Beautiful wood paneling has long been associated with traveling in style. In the 18th and 19th centuries, the finest horse-drawn carriages were embellished with highly decorative detailing, and as the wealthy moved to more ‘modern’ transportations the trend for rich wood paneling continued. The fabled Orient Express train carriages sported specially commissioned wooden marquetry and glass panels by the French designer René Lalique, while the ill-fated transatlantic liner Titanic had oak paneling throughout its first class cabins and a first class lounge covered with "boiseries" (paneling of carved wood). Cars also sported wood veneers, a tradition that has been continued to this day by a few luxury brands such as Rolls-Royce, aided by the advent of laser-cutting technology making the creation of intricate jigsaw-like marquetry less time consuming, while also opening up new design possibilities.
Earlier this year, Rolls-Royce unveiled the Pinnacle Travel Phantom from its Bespoke Collection, with a stunning example of marquetry dashboard design inspired by the era of epic journeys on luxurious trains.
“A journey in a Rolls-Royce Phantom draws parallels between a sumptuous and relaxing journey on a luxurious cross-continental train,” muses Gavin Hartley, Head of Bespoke Design, Rolls-Royce Motor Cars.
To evoke the stylized image of a train speeding across a landscape, the design uses 230 individual pieces of wood, combining the latest techniques with fine traditional craftsmanship. The impressive veneer motif was also applied to a number of other surfaces, from the glove box to the rear picnic tables and doors.
“The ability for us to draw on advanced technologies allows us to create a very accurate interpretation of an artwork. It provides us with precision and control when translating elaborate and intricate motifs into marquetry,” says Hartley adding, “the use of laser-cutting isn’t incorporated to save time; it allows us to ensure the inherent perfection of every Rolls-Royce motor car.”
Personalized marquetry has become one of the hallmarks of Roll-Royce whose skilled craftsmen and women can handle any customer requests, such as using wood from their own orchard. Some 17,500 wood veneer combinations are available for every Rolls-Royce and it all starts with the selection of that veneer – usually thinner than 1mm, that are obtained by either "peeling" the tree trunk or by thinly slicing from large rectangular blocks of wood known as flitches.
“We aim to get the best possible yield from a log. We use quite a lot of burrs which are rotary cut and peeled off the log, in a fashion not dissimilar to sharpening a pencil,” explains Jonathan Peedell, Woodshop Production Manager.
In the atelier of Rolls Royce
Tucked away on the ground floor at the Goodwood workshop, the Rolls-Royce veneer store houses an impressive array, ranging from elm and royal walnut to mahogany and olive ash burr. The room is a climate controlled humidifier held at a constant 25°C and 80 percent humidity “to keep the veneer soft and supple,” says Peedell.
“We need to make sure the product is flexible when we work with it, so we aim to put between eight to 10 percent hydration into the leaves of veneer, which is the level you would find when the veneer is cut from the log,” he adds.
Rolls-Royce’s wood specialist travels around the world to source veneer, “looking out for the characteristics that we want for a Rolls-Royce product: character and consistency,” says Peedell, adding, “Importantly, we don’t want any minerals in our veneer, which to the human eye will appear like a tiny grain of sand deposited inside the knot. These are quite common and most manufacturers will deal with this issue by staining their wood. But we don’t want our customers to have stained wood; when wood is stained you lose the reflective nature of the grain, which to the customer appears as a silky, reflective surface.”
“Because we don’t stain the veneer, it will continue to age as it dries out over time. I think it’s the only car in the world that continues to age, though I don’t think customers would notice the subtle changes,” he muses.
Bookmatching in the woodshop Goodwood
Each wood panel is composed of at least 58 laminated layers of tulip wood which are compressed tightly together. Tulip wood is chosen for its plain featureless aspect and comes from the poplar species, which makes it the perfect base, Peedell explains. “Tulip is what we call a straight grain wood, which means that when we press the layers together we will not trap any air pockets in any of the knots underneath,” he says. The latticework of veneer (straight grain vs cross grain) also helps to make it structurally rigid, as much as possible.
To this day, the Rolls-Royce workshop uses minimal machinery: a milling machine, “because no human being can do it better than that machine,” and the hot presses, “everything else is done by hand,” says Peedell.
The skilled workers will have to carefully match the veneer sheets - the technique is called book matching - , being able to visualize the final symmetry of the wood as it will run through the finished piece such as in a dashboard that will be composed of 46 pieces seamlessly joined together. The sheets of veneer will then be glued before the wood is meticulously sanded by hand to enhance the grain and finally, several coats of lacquer will add the final gloss in a process that takes at least one month.
In total, more than 200 people work in the Rolls-Royce woodshop producing more than 100,000 individual parts each year, and the artistic ways in which the craftsmen and women combine different veneers and inlays has long proven to be one of the most attractive and unique aspects of a Rolls-Royce interior.
As first published in Blouin Lifestyle Magazine.